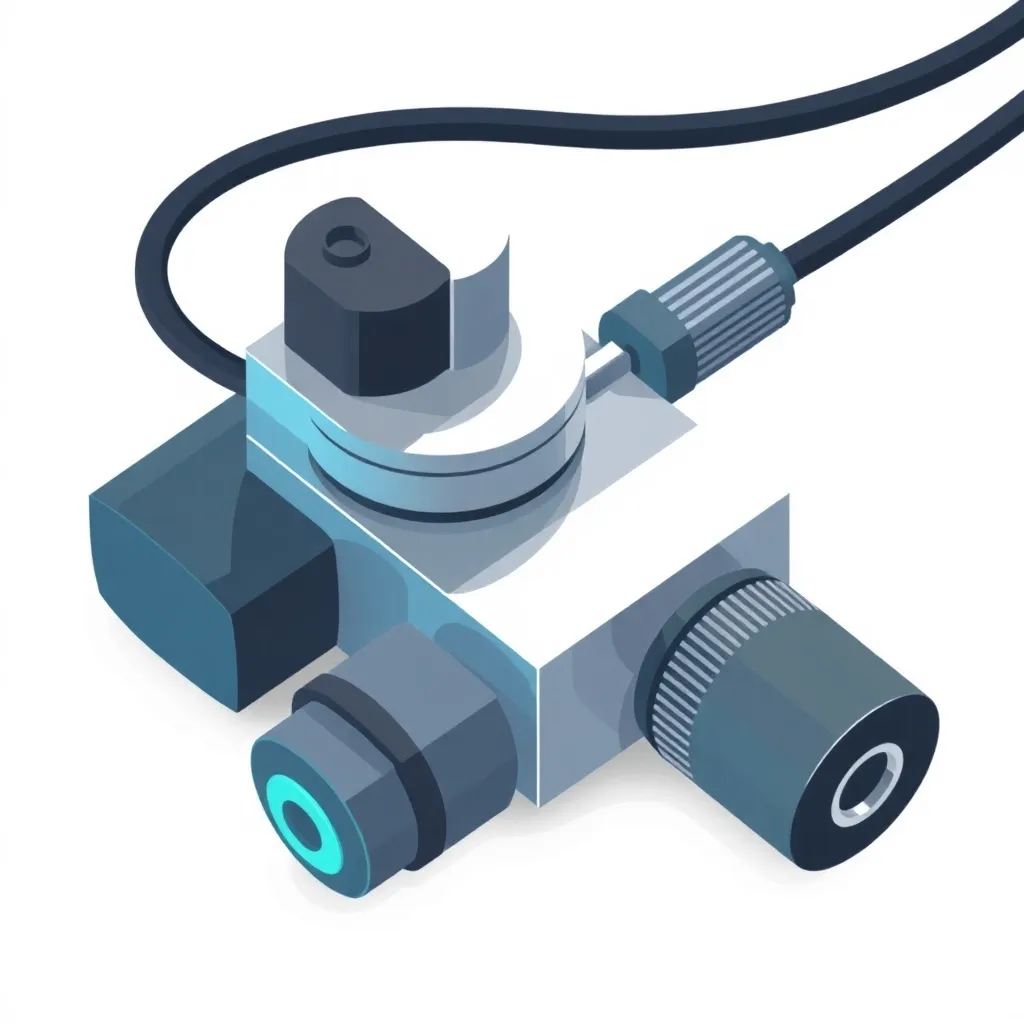
Датчики положения и угла
Датчики положения и угла являются неотъемлемыми компонентами систем измерения и контроля, обеспечивая точную информацию о пространственном положении механизмов, узлов и исполнительных органов. Эти устройства позволяют отслеживать линейные перемещения, угловые отклонения, скорость и направление движения. На основе этих данных строятся системы автоматизированного управления, контроля траектории, стабилизации и диагностики механических отклонений. Услуга включает подбор подходящих типов датчиков, проектирование схем измерения, установку, калибровку, интеграцию с программно-аппаратной инфраструктурой заказчика и последующее сопровождение.
Тип используемых датчиков зависит от задачи. Для линейных перемещений применяются индуктивные (LVDT), оптические, резистивные и магнитострикционные датчики. Угловые перемещения измеряются с помощью инкрементальных или абсолютных энкодеров, гироскопов, магнитных датчиков Холла и MEMS-сенсоров. В зависимости от условий эксплуатации выбирается форма сигнала (аналоговая, цифровая), диапазон измерений, разрешение, частота опроса, стойкость к загрязнениям и механическим воздействиям. Некоторые модели предназначены для работы в агрессивных средах, при вибрациях, перепадах температур и в условиях высокой точности позиционирования.
Инженерная подготовка включает выбор места установки, расчёт направлений перемещений, проектирование креплений и прокладку кабелей. Для обеспечения точности критично правильно ориентировать сенсор, минимизировать люфты, вибрации и паразитные воздействия. В случае подвижных соединений учитываются компенсационные элементы, гибкие муфты, защитные оболочки. Отдельное внимание уделяется заземлению, экранированию от электромагнитных наводок и защите от влаги и пыли. Некоторые типы датчиков требуют особого обращения при монтаже, включая строгие допуски на осевое и радиальное смещение.
Данные от датчиков положения и угла используются для управления приводами, регистрации отклонений от нормы, анализа динамики процессов и обратной связи в системах автоматизации. Программное обеспечение выполняет функции опроса, фильтрации, расчёта производных величин (скорость, ускорение), построения графиков, диагностики и сохранения истории. Возможна реализация интерфейсов визуализации, тревожных оповещений, синхронизации с другими измерениями и формирования отчётности. Интеграция с SCADA, HMI и ERP позволяет использовать данные положения как часть единого цифрового контура управления предприятием.
Типичные области применения включают мониторинг перемещений подвижных платформ, манипуляторов, транспортных тележек, рычажных механизмов, крано-балочных систем, рулевых приводов, а также элементов железнодорожного состава. В производстве датчики положения используются для отслеживания линейных подач, перемещений заготовок и корректировки положения инструмента. В железнодорожной отрасли они устанавливаются на тележках, рессорах, механизмах поворота кабины и в системах контроля положения токоприёмников. Использование таких датчиков позволяет обеспечить точность, безопасность и прогнозируемость функционирования сложных технических объектов.
Для обеспечения точности и надёжности необходима регулярная калибровка и техническое обслуживание. Проводятся процедуры начальной настройки, установка нулевой отметки, коррекция шкалы и проверка чувствительности. При эксплуатации в критических условиях выполняется периодический контроль сигналов, тестирование реакции на эталонные перемещения и диагностика работоспособности цепи. Отклонения фиксируются средствами самодиагностики, а при необходимости формируется уведомление о необходимости замены или перенастройки датчика. Поддержка включает замену элементов, обновление ПО, обучение персонала и помощь в модернизации.
Комплексная услуга по внедрению включает техническое обследование, подбор оборудования, поставку, монтаж, интеграцию в существующую инфраструктуру, разработку документации и последующее сопровождение. Датчики положения и угла становятся важнейшим звеном в системе управления и диагностики, обеспечивая непрерывный контроль над перемещениями и ориентацией оборудования. Их использование способствует снижению числа отказов, повышению точности технологических процессов и общему росту надёжности систем. Благодаря высокой адаптивности и широкому модельному ряду, решение может быть точно подстроено под специфику конкретного предприятия.