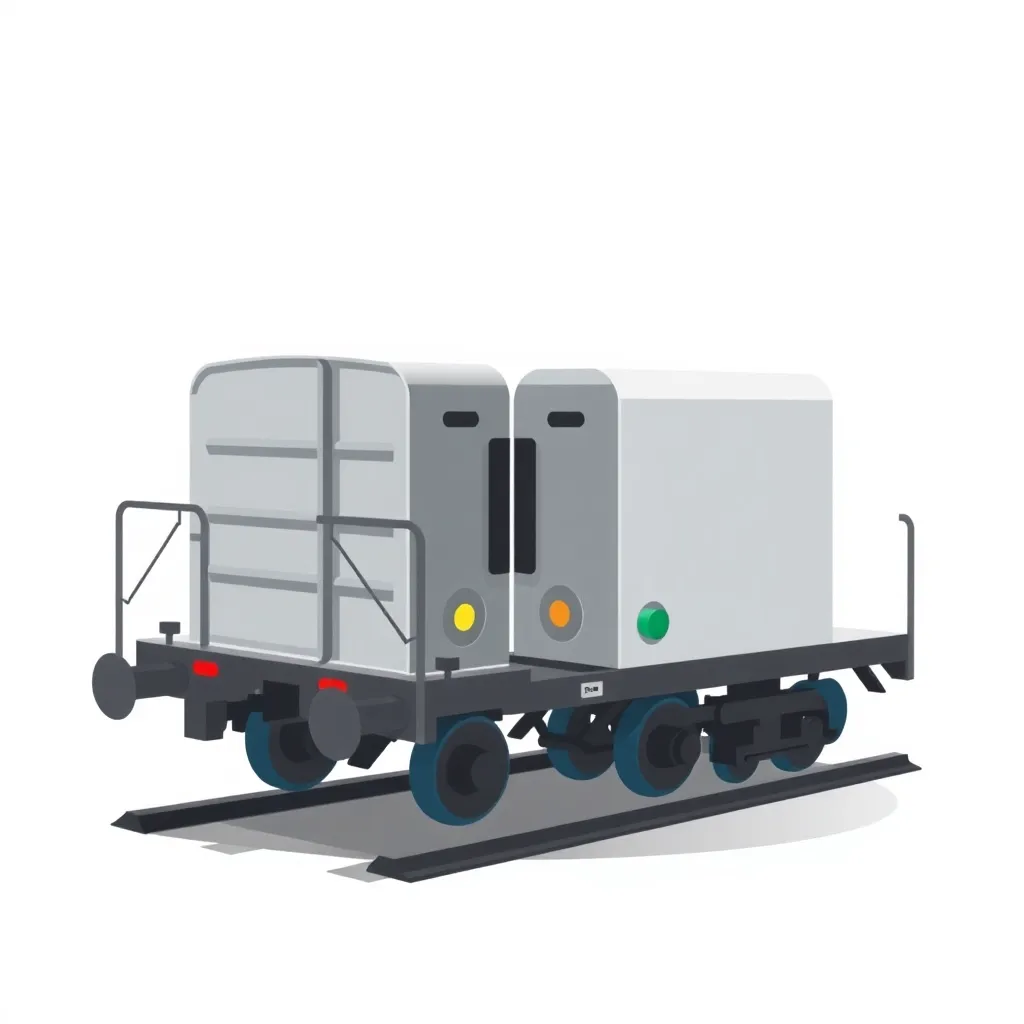
Тележки и сцепные устройства
Проектирование тележек и сцепных устройств представляет собой важнейшее направление в создании надёжного и безопасного подвижного состава. Тележка — это несущий элемент, обеспечивающий опору вагона, передачу вертикальных и горизонтальных нагрузок, а также реализацию плавного и устойчивого хода. Сцепные устройства, в свою очередь, обеспечивают механическое соединение между вагонами и передачу тяговых усилий поезда. Эти два компонента непосредственно влияют на эксплуатационные характеристики, безопасность движения и комфорт пассажиров. Проектирование начинается с анализа технических требований, включая тип вагона, максимально допустимую нагрузку на ось, радиусы кривых, скорости движения и условия эксплуатации.
Конструкция тележки включает раму, буксы, рессорное подвешивание, амортизаторы, тормозное оборудование и элементы крепления колёсных пар. Каждая из этих подсистем должна быть рассчитана на многократные нагрузки, вибрации и удары, возникающие в процессе движения. В современных проектах широко используются двухосные тележки различных серий, соответствующие требованиям ГОСТ, МПС и TSI. Инженеры выполняют прочностные и динамические расчёты, определяют точки концентрации напряжений, анализируют поведение конструкции при различных скоростях и нагрузках. Особое внимание уделяется конструкции букс и элементам демпфирования, от которых зависит устойчивость движения и уровень вибраций. Также рассчитывается угол поворота тележки в кривых участках и взаимодействие с рельсовым путём.
Сцепные устройства проектируются с учётом передаваемых усилий при трогании, торможении и аварийных режимах. Наиболее распространённой является автосцепка, которая позволяет автоматически соединять вагоны и гасить динамические удары. Конструкция включает корпус, замковые устройства, поглощающие аппараты и элементы привода. На этапе проектирования проводится расчёт прочности элементов сцепки, анализ ударных нагрузок и определение оптимальных характеристик поглотителей энергии. Также разрабатываются элементы, обеспечивающие безопасность при расцепке и защиту от самопроизвольного разъединения. В зависимости от типа подвижного состава могут применяться разные стандарты сцепления, в том числе совместимые с зарубежными системами.
Важной задачей является обеспечение взаимозаменяемости и ремонтопригодности узлов тележек и сцепных устройств. Конструкции разрабатываются с учётом существующей ремонтной базы, наличия оборудования и инструмента на депо. Узлы проектируются модульно, что упрощает их замену и обслуживание. Применяются стандартные посадочные размеры, резьбовые соединения, быстросъёмные элементы. Допускается возможность применения альтернативных материалов при ремонте без ухудшения характеристик. Документация включает указания по техническому обслуживанию, периодичности проверок, допускам износа и методам восстановления работоспособности. Это снижает затраты на жизненный цикл изделия и повышает его эксплуатационную готовность.
Особое внимание уделяется технологичности производства. Конструкции тележек и сцепных устройств адаптируются под существующее оборудование на машиностроительных предприятиях. Используются сварные и литьевые компоненты, элементы холодной и горячей штамповки, а также механической обработки. Оптимизируется количество деталей и типоразмеров, снижается вес без ущерба прочности. Внедрение цифровых моделей (CAD), автоматизированной сборки и контроля качества позволяет обеспечить точность и стабильность параметров. На этапе подготовки производства разрабатываются оснастка, контрольные шаблоны и методы испытаний. Это ускоряет переход от проектирования к изготовлению и снижает брак.
Проектирование сопровождается разработкой полного комплекта технической документации: чертежей, спецификаций, расчётных пояснений и инструкций по сборке. Документация создаётся в соответствии с ЕСКД и международными стандартами, с возможностью интеграции в PLM-системы заказчика. Также формируются 3D-модели для визуального анализа и проверки сборки, а при необходимости — анимации для демонстрации работы механизмов. Все элементы проходят проверку на технологичность, соответствие техническому заданию и возможность сертификации. При необходимости проводится согласование с внешними экспертными организациями и сертифицирующими органами.
После завершения проектирования тележки и сцепные устройства проходят лабораторные и стендовые испытания, включая тесты на прочность, износостойкость, устойчивость к ударным нагрузкам и вибрации. Проверяется точность посадки, взаимодействие с другими элементами вагона, надёжность сцепления и поведение в аварийных режимах. На основе результатов испытаний возможно внесение корректировок в конструкцию. Готовые изделия проходят сертификацию и могут быть запущены в серийное производство. Проектная команда при необходимости сопровождает внедрение, участвует в пусконаладке и сборе данных в реальной эксплуатации. Такой подход обеспечивает высокое качество, надёжность и адаптацию изделий к условиям современного железнодорожного транспорта.