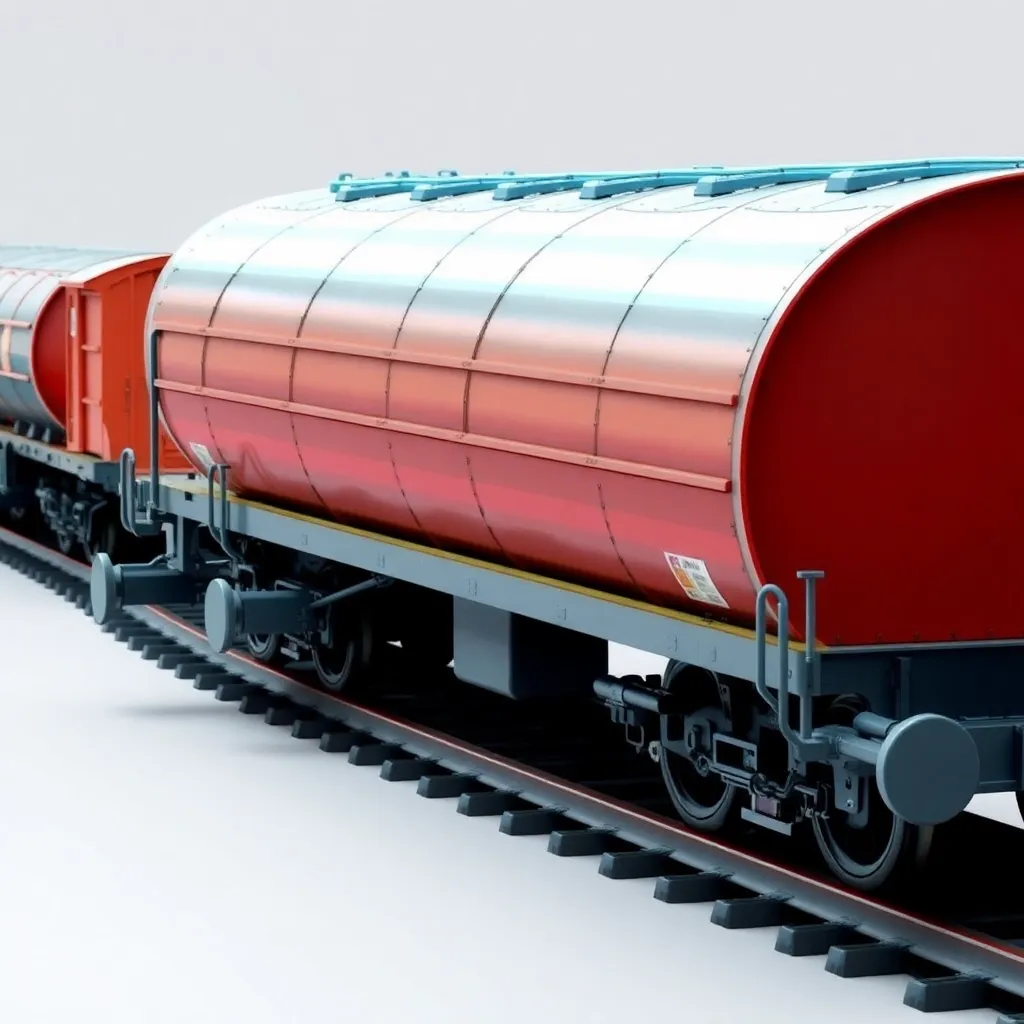
Грузовые вагоны
Проектирование грузовых вагонов требует комплексного инженерного подхода, учитывающего специфику перевозимых грузов, условия эксплуатации, требования к надёжности и соответствие нормативной базе. Каждый тип грузового вагона — будь то полувагон, платформа, цистерна или хоппер — создаётся под конкретные задачи и стандарты эксплуатации. На начальном этапе проводится анализ грузопотоков, географии маршрутов, температурных режимов и технических ограничений инфраструктуры. Это позволяет заложить в проект прочную конструктивную основу и определить допустимые нагрузки на ось, массу тары и габариты. Кроме того, важно предусмотреть возможность взаимодействия вагона с различными средствами погрузки и выгрузки, в том числе автоматизированными.
Одной из ключевых задач является подбор и конструирование кузова, который обеспечивает не только размещение груза, но и его сохранность в пути. Для этого используются как цельнометаллические, так и каркасно-панельные конструкции с защитой от влаги, пыли, механических повреждений и агрессивной среды. Типовая конфигурация может включать боковые или торцевые двери, люки, сливные устройства, крышки и амортизаторы. Отдельно прорабатываются элементы жёсткости и усиления, а также возможность крепления груза в соответствии с правилами перевозки. Проект учитывает как возможности ручной загрузки, так и механизированной, с учётом наличия кранов, грейферов и конвейеров на терминалах. Также предусматривается удобство для очистки и технического обслуживания внутреннего пространства.
Подвеска и тележки — важнейшие элементы грузового вагона, отвечающие за его плавность хода, надёжность и безопасность. Они проектируются с расчётом на допустимую нагрузку, динамику движения и стойкость к износу. В зависимости от типа вагона могут использоваться двухосные и четырёхосные тележки различных серий. Обязательной частью проектирования является расчёт вибраций, усталостной прочности и параметров движения на участках с различным профилем пути. Также рассматриваются вопросы уравновешивания нагрузки между осями, особенно при неравномерной загрузке. Кроме того, учитываются требования к взаимодействию с тормозной системой состава и возможность применения автоматических тормозных систем.
Современные проекты всё чаще включают элементы автоматизации и цифровизации. Это могут быть датчики нагрузки, системы мониторинга положения, контроля вскрытия люков, контроля температуры или состояния груза. Такие решения требуют внедрения дополнительных кабельных трасс, источников питания и модулей связи. Уже на стадии проектирования важно предусмотреть резервные каналы, защищённые зоны размещения электроники и устойчивость компонентов к вибрациям и климатическим условиям. Электронные компоненты проектируются с учётом быстрого обслуживания и замены, без необходимости разборки основных конструктивных узлов. Такие дополнения повышают интеллектуальный уровень вагона и его ценность в логистических цепочках.
Материалы конструкции отбираются с учётом условий эксплуатации: устойчивость к коррозии, нагрузкам, абразивному воздействию и перепадам температур. Наиболее распространены низколегированные стали, защищённые специальными лакокрасочными покрытиями или цинковыми слоями. Возможны варианты с использованием алюминия и композитов в неответственных зонах. Покрытия разрабатываются с учётом агрессивности среды — от обычных маршрутов до химически активных или прибрежных участков. Также анализируется поведение материалов при длительном воздействии статических и переменных нагрузок. Производится расчёт остаточного ресурса и закладываются меры по его увеличению, включая возможность замены отдельных элементов без полной разборки вагона.
Конструкторская документация включает в себя полный комплект чертежей, расчётов, спецификаций и пояснительных записок. Каждый проект проходит внутреннюю проверку, согласование с производственными цехами, сертифицирующими организациями и, при необходимости, заказчиком. Документация формируется в цифровом виде с привязкой к моделям САПР, что облегчает управление изменениями, сопровождение производства и контроль качества. Дополнительно могут разрабатываться электронные паспорта вагона, в которых фиксируются параметры, даты обслуживания, проведённые ремонты и статус сертификации. При необходимости документы подготавливаются для интеграции с внешними информационными системами логистики или учёта.
После завершения проектирования создаются опытные образцы или макеты для проверки технических решений. В рамках приёмочных испытаний оцениваются прочность, надёжность, маневренность, герметичность и удобство эксплуатации. При необходимости вносятся корректировки в чертежи и перечни материалов. Также возможна адаптация проекта под требования зарубежных рынков — по ширине колеи, сцепке, тормозным системам и знакам маркировки. Готовое изделие после испытаний и сертификации может быть передано в серийное производство, включая сопровождение и техническую поддержку на этапе внедрения. Такой подход позволяет обеспечить не только выпуск конструкции, но и её реальную готовность к эксплуатации в жёстких условиях грузоперевозок.